June 20th, 2022
Bessac completes the work on the first tunnel built entirely with Ultra Low Carbon concrete pipes under the EXEGY brand
Remember that at the end of 2021 we presented this world-first from Bessac – a treated water discharge tunnel built using ultra-low-carbon concrete pipes under the brand EXEGY by Bessac. Let’s take a look back at this unprecedented project that has just been completed and demonstrates Soletanche Bachy’s expertise in low carbon concrete.
- Design-build of the treated water discharge tunnel for the Bonneuil-en-France wastewater treatment plant
- 304 jacking pipes prefabricated using an Ultra Low Carbon concrete solution under the EXEGY by Bessac brand
- An environmental project in its design
- Contract amount: €7.8 million
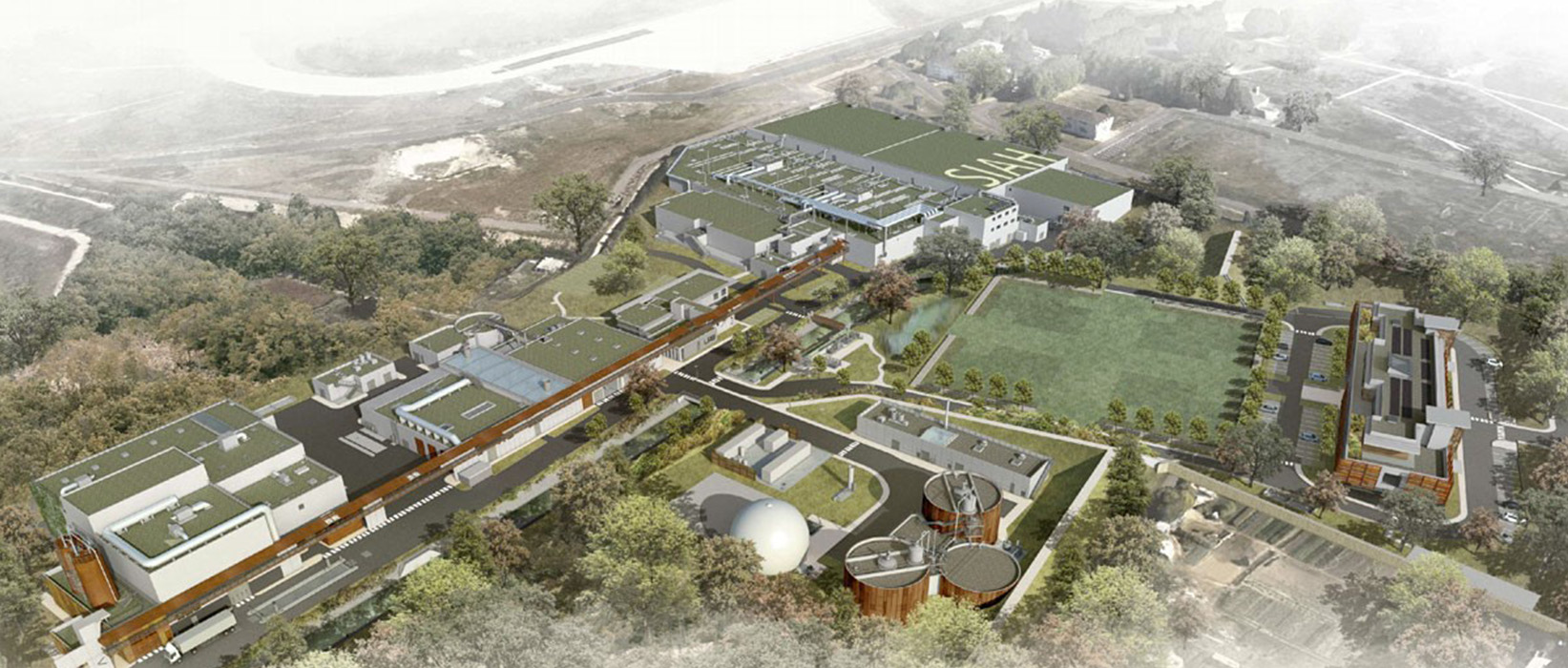
Creating a “bespoke” concrete with impressive characteristics!
Technically, the project involved developing a “bespoke” concrete formulation for the worksite, while using locally available materials.
There was also a desire to obtain an Ultra Low Carbon concrete formula, i.e. one achieving the highest level of carbon footprint reduction in its specific compressive strength category (<140 kgCO2eq./m3 for a C50/60), while allowing its reuse on projects with different specifications.
In addition to these requirements in terms of performance and robustness, there were also some major technical constraints:
- Significant mechanical stresses during implementation (625 tonnes of shearing force, requiring a C50/60);
- Guaranteed productivity: more than 15 MPA of resistance necessary from the outset in order to handle 7.2-tonne pipes;
- Guaranteed durability of the concrete, particularly in terms of the sulphates in the ground and the potential acidity of the effluents;
- A self-levelling concrete, to meet the cost-control and end-quality objectives, while facilitating implementation;
- Consistent environmental performance in the manufacturing process: limited heat treatment and local materials.
Traditional blast-furnace cement solutions (CEM III) failed to produce a concrete suitable for jacking pipes in such a demanding project environment and able to go as far in reducing the CO2 impact.
Thus, a specific formula has been developed. The concrete’s suitability has been validated by durability tests, particularly to justify its transfer properties (chloride diffusion of less than 10-12m2s-1) and its resistance to acids (test of leaching at pH 4.5).
Finally, this formula certainly earns its place in the Ultra Low Carbon concrete category, since it records just 84kgCO2eq./m3.
Its emissions are therefore four times lower than concrete formulas generally used for the prefabrication of jacking pipes.
An EXEGY by Bessac innovation in the field of low-carbon concrete
The SIAH (Syndicat Intercommunal pour l’Aménagement Hydraulique des Vallées du Croult et Petit Rosne) has entrusted the consortium comprising Bessac (as lead company), Soletanche Bachy Fondations Spéciales and Setec Hydratec, with the design and build of a treated water discharge pipeline from the new wastewater treatment plant to its connection with the Garges-Épinay collector.
To build this structure, which will improve water management, Bessac is carrying out a world first: building the entire tunnel with ultra-low carbon concrete pipes. The concrete formula has a quarter of the carbon footprint of the concretes generally used for the prefabrication of jacking pipes. This project is carried out under the EXEGY by Bessac brand, which combines all Bessac’s and Soletanche Bachy’s expertise in low-carbon concrete.
This technical feat has been made possible by:
- The nature of the design-build contract, which enabled the development of a bespoke formulation for the worksite using locally available materials.
- SIAH’s desire to participate in a strong environmental approach.
- Bessac’s certified competence, both in the boring of tunnels and the design and prefabrication of jacking pipes.
- The involvement of Soletanche Bachy’s integrated materials laboratory, which led to the development of a specific concrete formulation.
- Lastly, support from the Tunnel Factory, which helps drive tunnel innovations for the various VINCI Construction entities.
For Bernard Théron, President of Bessac,
“Traditional blast-furnace cement solutions (CEM III) failed to produce a concrete tailored to the technical constraints of jacking pipes and able to go as far in reducing the CO2 impact. That is why we have developed a specific formula and carried out a durability test protocol to validate its suitability for use and its resistance to acids.”
Bessac is also taking the approach even further by having its Ultra Low Carbon pipes prefabricated close to the site, in the Capremib factory near Reims. Benefiting from Bessac’s expertise in pipe prefabrication, this partnership has made it possible to reduce pipe transport distances and the associated carbon footprint.
This project is part of Soletanche Bachy/VINCI Construction’s environmental commitment to reducing the carbon footprint of its worksites by 20% by 2030, particularly by tackling cement consumption (scope 3), and by 40% by 2030, by reducing fuel and energy consumption (scopes 1 and 2).
An optimised and environmentally-oriented design
The project designed by Bessac also addresses the challenges of preserving biodiversity and natural spaces. The work is taking place in an area that includes natural spaces classified as NATURA 2000 zones, such as the Parc de la Courneuve and the wetlands of Morée and Croult, which constitute real centres of biodiversity for protected species.
The design phase and its entire implementation have been designed by Bessac to limit the environmental impact of the work:
- Installations for digging the microtunnel’s entry shaft were relocated to the site of the Dugny CTR (technical regulation centre) rather than to the Natura 2000 area of the La Courneuve park.
- Creation of the pipeline in a single 911 linear metre section of DN 1600.
- Drastic reduction in the number of intermediate shafts and optimisation of the secant-pile foundations, which made it possible to reduce the quantities of materials used on the project.
Work carried out to the millimetre
In addition to an optimised design and technical and logistical challenges, particularly due to the compact size of the site, the presence of networks and sensitive structures also needed to be taken into account.
For the construction of a watertight retaining structure, Soletanche Bachy Fondations Spéciales used the Starsol® process, which allowed the earthworks and the excavation from the water table.
Digging by the tunnel-boring machine required meticulous analysis and organisation. Having successfully bored through the secant-pile and fibre-glass wall, the microtunnel machine and the pipeline push ahead under the thrust applied by the thrust frame installed in the working shaft. The force passes through the pipe sections that have been laid as the microtunnel machine moves forward. To limit friction, a lubricating mud is injected into the annular space of the borehole via nozzles placed at the rear of the microtunnel machine and via the jacking pipes.
Finally, logistics was a real day-to-day challenge, in order to ensure the continuous production of the microtunnel machine. Pipe deliveries and rubble evacuation trucks moving in and out of the site have been precisely measured, given the limited storage space available on the surface and the imposed truck rotation route on the CTR site.
A remarkable arrival at the exit shaft
On 10 May 2022, the microtunnel machine called Nicole bored through the wall of the exit shaft nearly three months ahead of the project’s contractual schedule. This is a great success and accomplishment for the Bessac teams, who worked on this jacking project with energy and enthusiasm.
This arrival provides a fitting conclusion to the boring of 912 linear metres of tunnel, which will eventually connect the new wastewater treatment plant in Bonneuil-en-France to the Garges-Epinay collector in Dugny.
This project has seen several accomplishments:
- Record distance travelled: 912 linear metres à Longest section ever laid in France with a DN1600 diameter
- Three months of jacking work: average of approximately 300 linear metres/month achieved by the project in two shifts
- 100% Ultra Low carbon Concrete pipes: a world first, with the entire tunnel equipped with EXEGY by Bessac Ultra Low Carbon Concrete.
The teams will now refocus on dismantling the tunnel equipment and removing the jacking installation so that the project’s civil engineering works can be finalised
Finally, this project was awarded the FSTT trophy in the Innovation category on 31 May 2022. A great recognition from the profession!
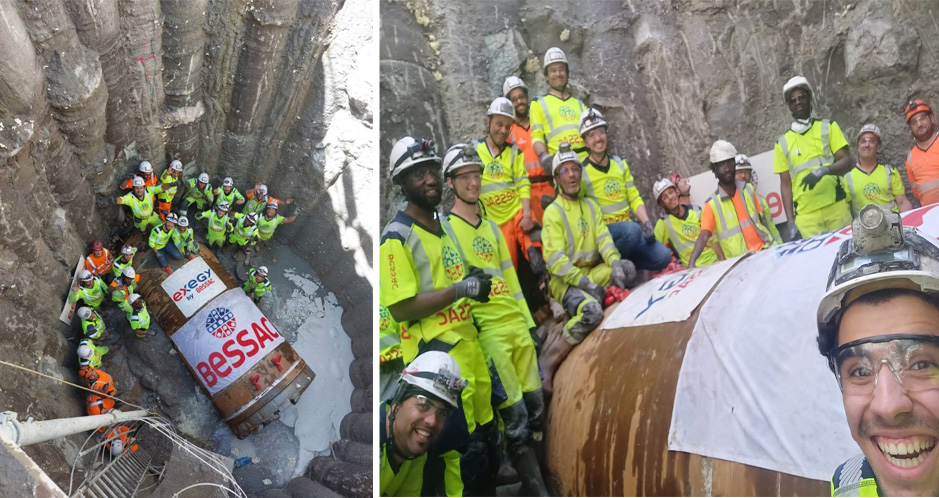