September 19th, 2022
From our workshops in France to Indiana (USA) – the compact Hydrofraise® with grippers crosses the Atlantic!
Equipment | Interview | News | Testimonies
After its construction by the The Equipment Manufacturing & Engineering Department in France, the HC05® arrived at a diaphragm wall worksite, in Indiana (USA), at the start of July. How can transportation of such a large machine to the other side of the world be organised and optimised to ensure that it is operational on-site within the deadline? This is precisely one of the many advantages of the Soletanche Bachy model : Local entities supported by a team of experts, capable of intervening anywhere in the world. We find out more about this epic feat, with Jade Van Klaveren, Head of Purchasing, Logistics and Export Department.
Transporting a large machine across oceans involves careful planning. It is a job for professionals, requiring significant expertise at each of the many stages in the shipping process. This is the role of the Technical Department’s Purchasing, Logistics and Export team.
“During the initial phase of an equipment shipping project like this one, we study the feasibility, the context and the solutions available to us to ensure the safest, most reliable, fastest as well as the most inexpensive shipment,” says Jade Van Klaveren.
Planning: numerous constraints to anticipate
A large number of formalities and administrative requirements need to be taken into account from the outset.
Firstly, due to the destination. Road transport is subject to a lot of restrictions in the United States. These vary from state to state, placing a major burden on the project. In Indiana, loads must not exceed 77 tonnes in weight and 4.10m in height. The HC05® weighs 80 tonnes and is 4.21m high however.
“Faced with these constraints, we have imagined many solutions,” continues Jade Van Klaveren.
- “Remove the rollers to reduce weight? There would still be the height problem.
- Remove the tracks? This would reduce weight and height, but prevent the machine from being mobile. A lifting beam would therefore be needed and unfortunately only one exists in the Group, currently in France.
- Completely dismantle the machine and containerise it? We would then face the problem of the current global container shortage, particularly in the United States. Especially since there is currently a two to three month wait for availability of containers and space on ships, which is very long compared with lead-times of approximately two weeks before the Covid crisis.”
Packaging and transport: finding the best time/cost compromise.
“We eventually found a solution,” says Jade Van Klaveren. “Dismantling the HC05® without putting it in a container, but instead putting it on MAFI trailers (roller trailers), bolsters or even leaving items bare, for loading onto RO-RO (roll-on/roll-off) ships. This solution avoids road transport restrictions in the United States, while also overcoming the container shortage.”
A total of two MAFI trailers, one 20ft bolster and four bare packages were loaded at the port of Zeebrugge in Belgium, with the ship’s departure scheduled for 30 May. This date was brought forward to 24 May, however, forcing the Purchasing, Logistics and Export team to finalise preparations for sending the machine within very tight deadlines.
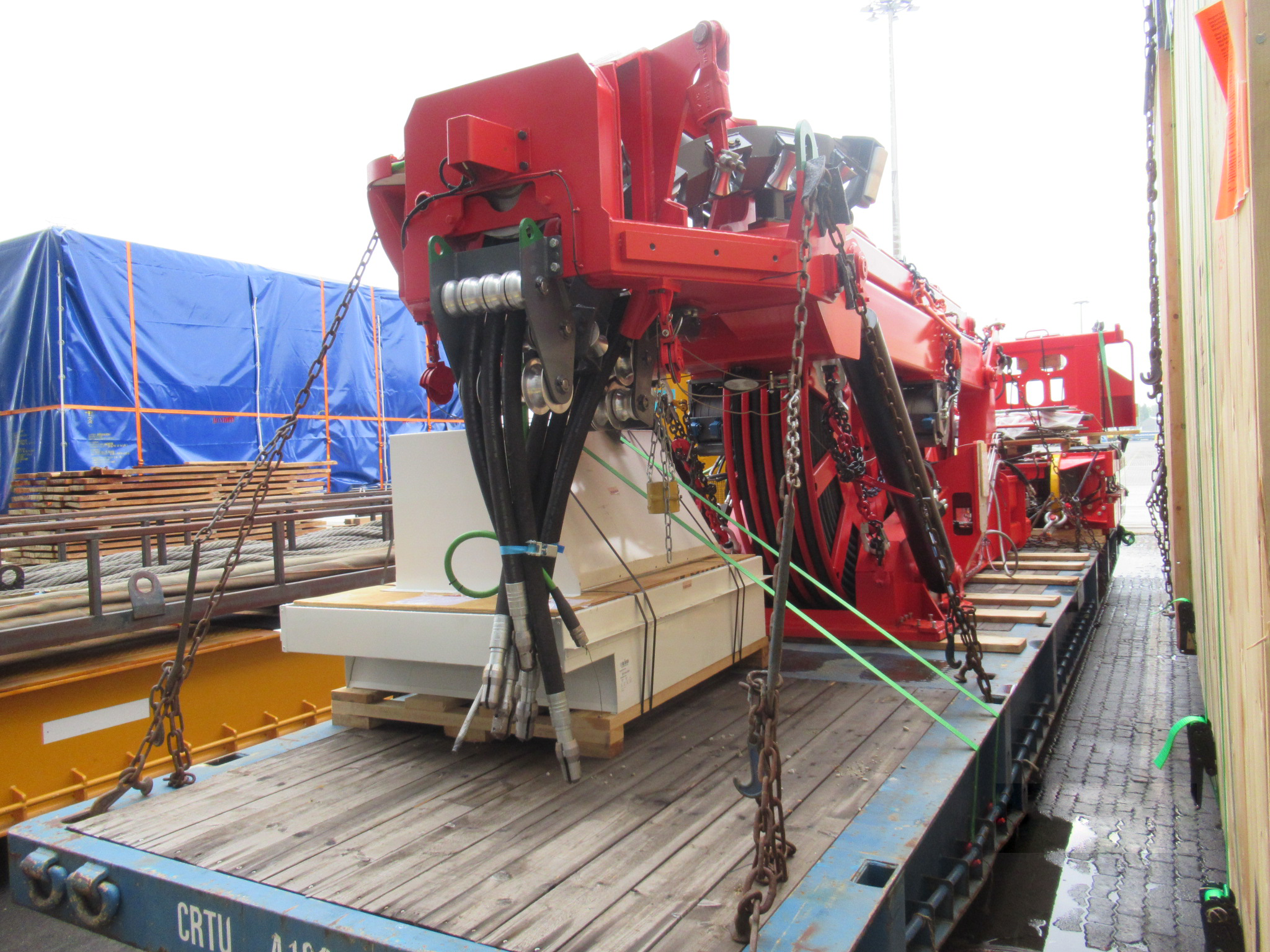
A custom-made packaging made by our carpentry.
This is when the team’s expertise comes into play, in order to prepare bespoke packaging for the various parts of the machine. The aim is to protect equipment from the risks of the journey and to mark each component with its name/dimension/weight – complete information to allow easy identification during transhipment and assembly.
Once all the parts had been delivered to the port, a marine surveyor was present during loading and prepared an inspection report attesting to the condition of the parts after loading, as well as the quality of their blocking and bracing.
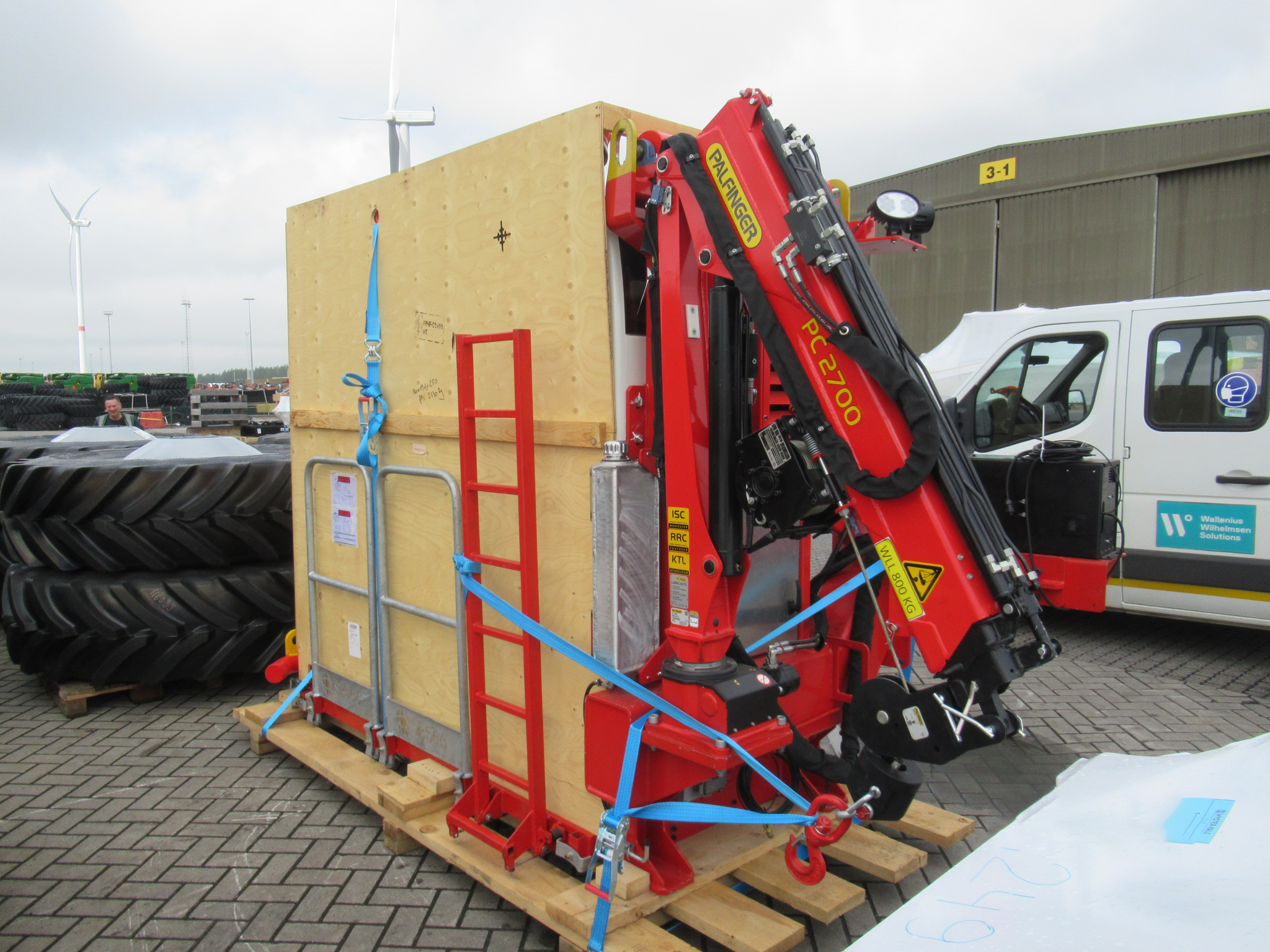
Final destination: The diaphragm wall site in the United States
Once the trailers had been loaded, they set off for their final destination, the port of Savannah in the southern United States. “We faced maritime transport risks, since the ships had to stop at other ports before Savannah, particularly New York, which turned out to be congested. The ship was stuck there for over a week, which delayed its arrival. We are also dependent on weather conditions, which can impact delivery times.”
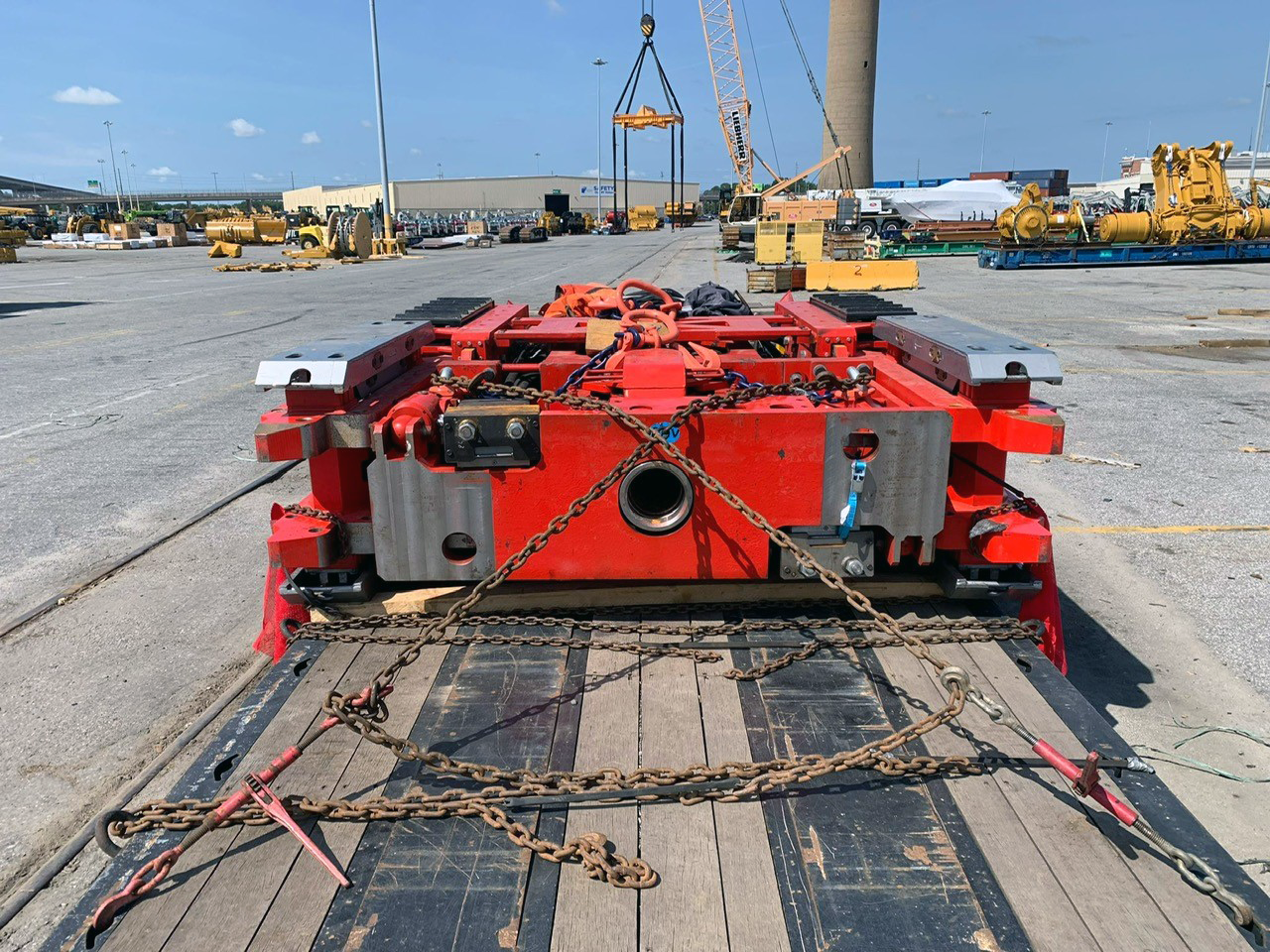
Administrative and customs follow-up, a key expertise in logistics and export of equipment.
Another of the Purchasing, Logistics and Export team’s key areas of expertise is administrative supervision. “If a document is missing or completed incorrectly, a shipment can be refused entry to a country or be held up for a long time in customs,” explains Jade Van Klaveren. The administrative teams therefore prepared the export invoices, packing list and export customs document.
Its strong anticipation of needs, especially in the current context, enabled the Purchasing, Logistics and Export team to ensure safe delivery of the equipment, which arrived at its destination on time at the start of July! The machine was then reassembled by Nicholson Construction’s teams on-site. The experts who built the machine also continued to provide support,by proving to the worksite teams a training on-site.
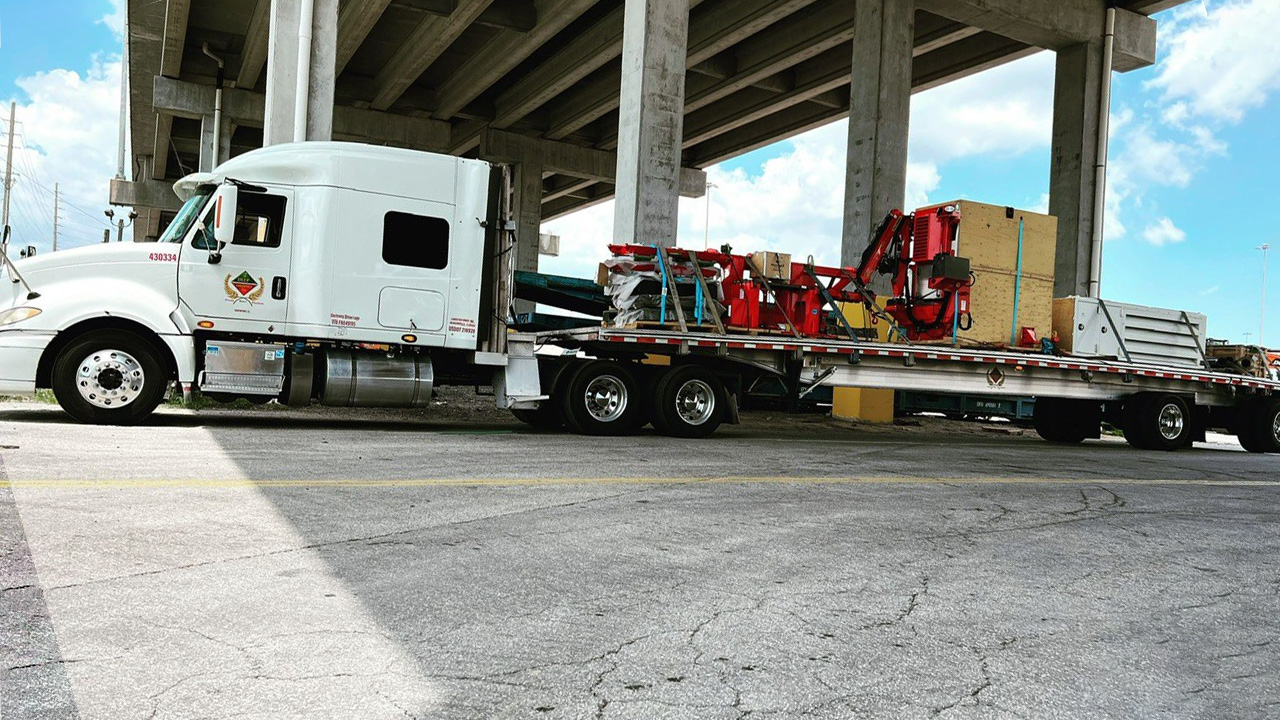
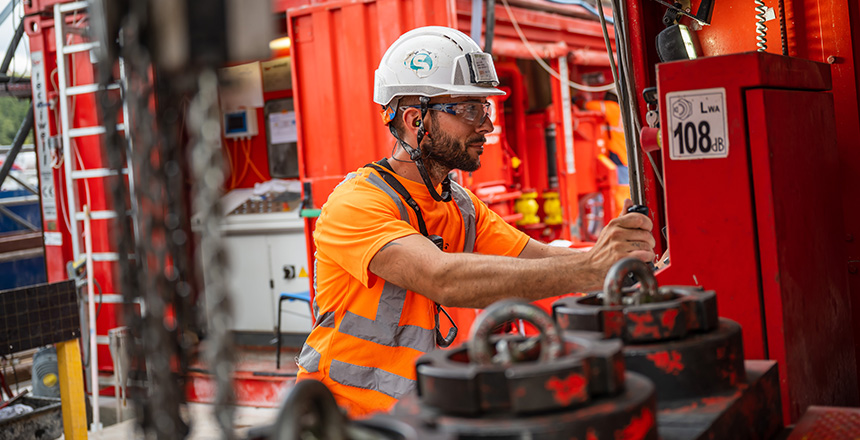
Local teams that rely on the expertise of a Group
This is one of the strengths of the Soletanche Bachy group, world leader in foundations and soil technologies: From tenders to execution of the project, local subsidiaries present all over the world can rely on our centralized teams, experts in design-manufacture of equipment, in logistics, methods, digital and also in fleet management and grout and concrete formulation, to provide them the best solutions for the projects we work on.