Project Description
Cost-effective and more eco-friendly structures
The Geomix® process uses the soil mixing technique across a broad spectrum of applications, including soil improvement, retaining walls or cut-off walls: a technique well understood by the teams of Soletanche Bachy.
What is Geomix® ?
The Geomix® process combines the Deep Soil Mixing technique with Hydrofraise® technology to build in situ soil-cement elements of rectangular cross section.
The technique uses two pairs of rotating drums to destructure the soil while combining it with a cement grout. This equipment is compatible with many types of base carriers making it particularly flexible in use. This type of equipment is also known as CSM (Cutter Soil Mixing).
The soil/cement mixture can reach an average compressive strength of 6 MPa and hydraulic permeability values below 10-6 cm/s.
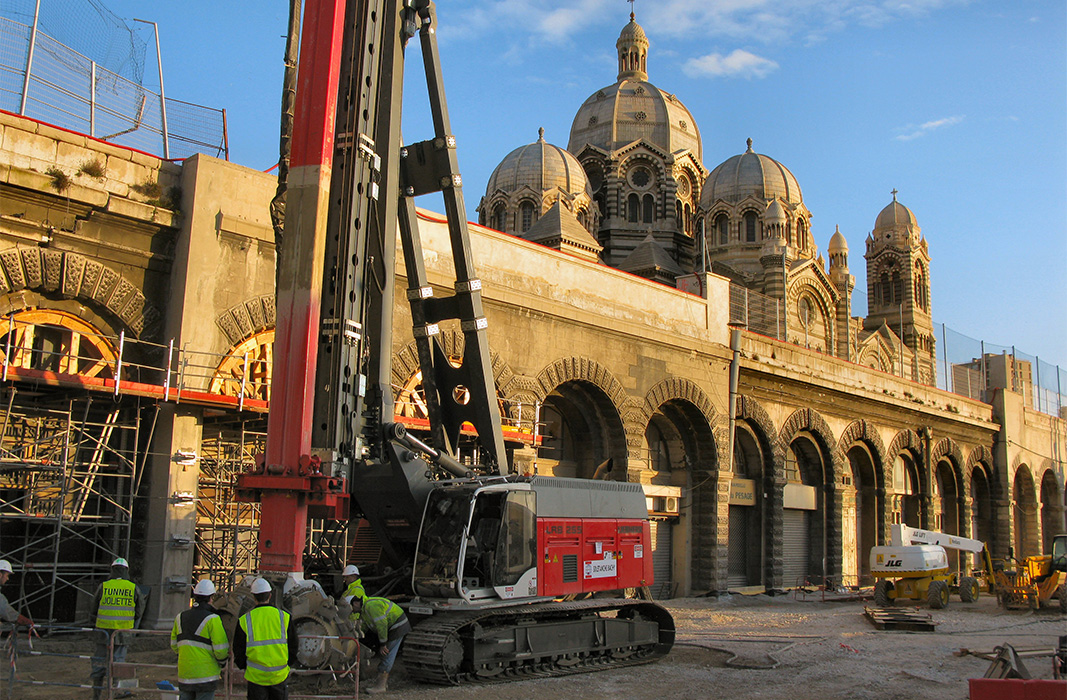
What are Geomix® applications?
The Geomix® process is used to form soil/cement barrettes in a single bite.
Continuous walls can be created by a succession of overlapping bites, built following a primary secondary sequence.
Used without structural reinforcement, the resulting walls can form low permeability barriers or be used for ground improvement purposes, such as slope stabilisation and liquefaction mitigation.
Temporary or permanent retaining walls can be created when combined with structural reinforcement, usually in the form of metal profiles incorporated into the mix.
Wall dimensions
As with a Hydrofraise® wall, the wall thickness corresponds to the width of the drums used to create it: these range from 500 mm to 1,200 mm.
What are the advantages of this technique?
A more economical support of excavation solution beneath groundwater level
A patented solution for the construction of permanent retaining structures
Real-time control of verticality
Cut-off walls with lower permeability than slurry walls
No heavy handling of rebar cages
No vibration during the process
Can be used within less than one metre of existing structures
Saves time as it is often unnecessary to build guide walls
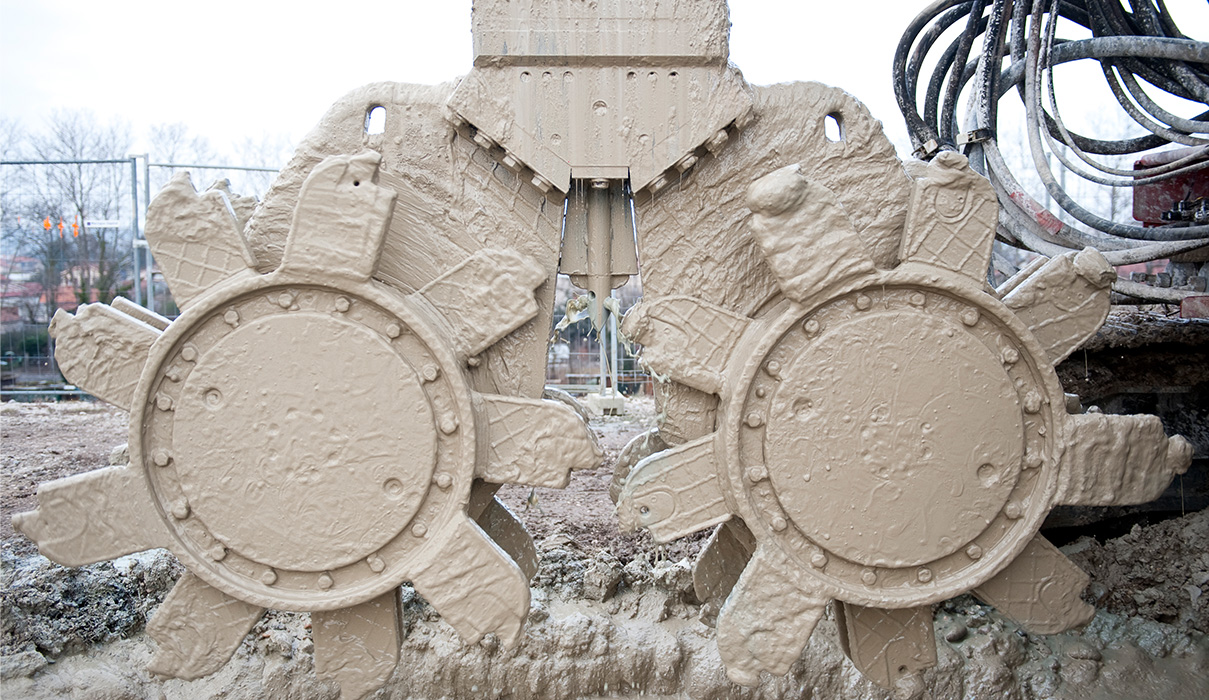
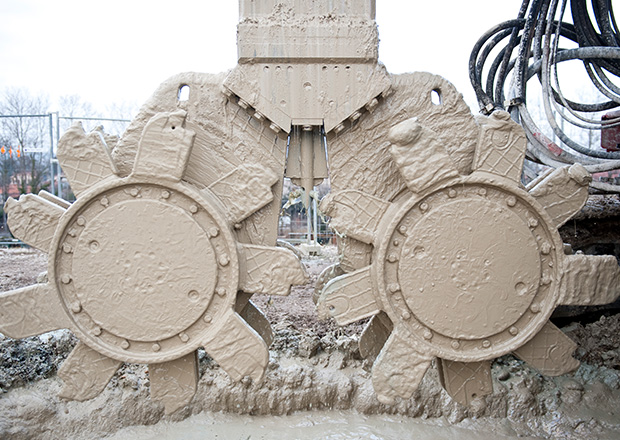
How is the Geomix® process implemented?
Geomix® is a 2-phase process.
A downward phase to destructure the soil and an upward phase to homogenise the mix. The grout binder can be incorporated during either of these two phases.
For support of excavation purpose, Geomix® walls usually incorporate structural reinforcement to counteract the bending forces due to earth pressure. These profiles are inserted into the fresh mix. The soil/cement material is stressed in compression arches between the profiles. The very low permeability of the material protects the excavation from water ingress through the wall.
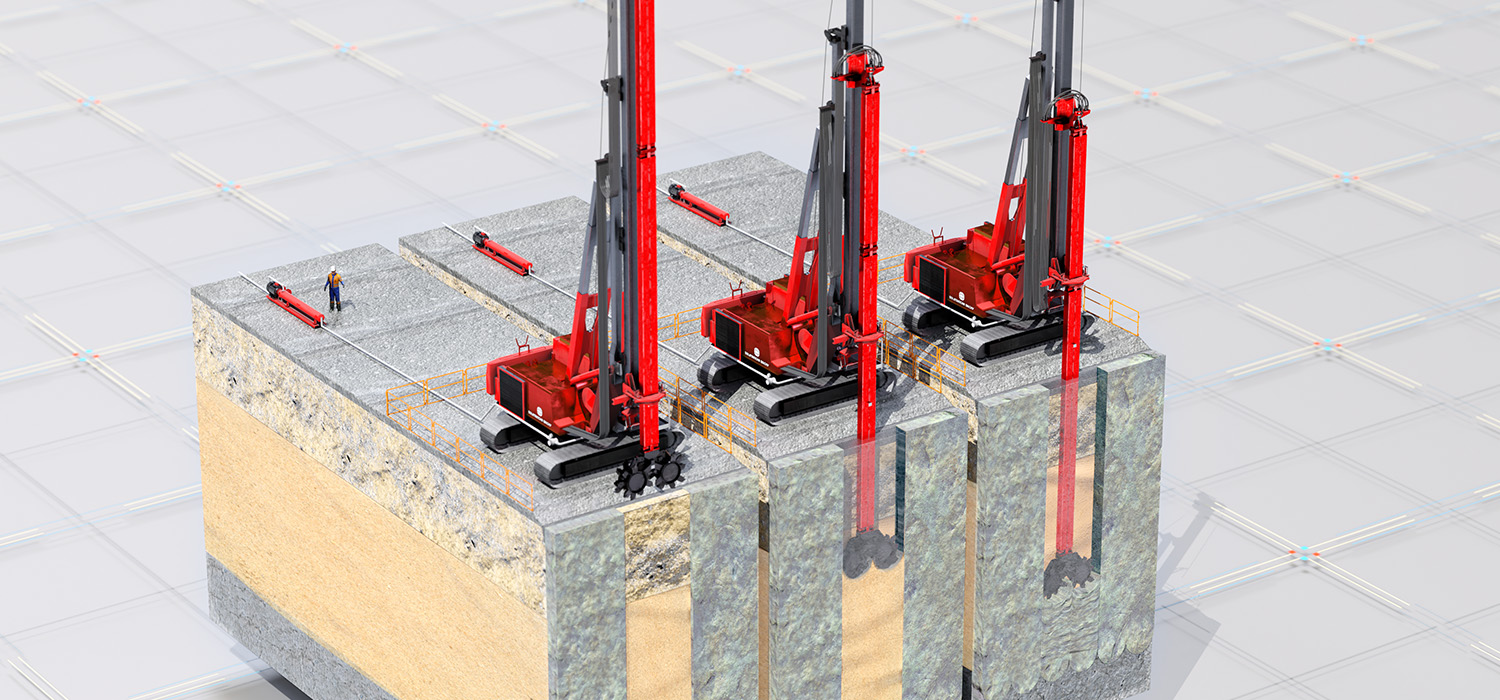
Soletanche Bachy’s advantages
Execution controls and monitoring
Geomix® walls are checked and monitored at various stages of their construction and at different levels:
– Regular monitoring of grout properties and grout design
– Real-time rig positioning and real-time verticality controls
– A dedicated supervision system embedding the latest data transmission technology, checking simultaneously the mix homogeneity and the quantity of binder incorporated.
– Properties of the final material can be checked by sampling the fresh mixture and/or core drilling
Did you know ?
The Geomix® process has been used for many applications… urban excavations, shafts, cut-off walls, quay repairs, liquefaction mitigation, TBM break in/break outs, soil improvement, etc. … and in many business sectors, from residential and commercial buildings to industrial facilities, public landfill sites, road and subway tunnels, airports and nuclear power plants.
Many Geomix® projects have been completed in recent years: