02/12/2020
Soletanche Polska has just finalised the project’s highly technical work: Norbling Factory
By 2030, Warsaw wants to become a “short distance” city, with more accessible areas, less congestion, thus reduce the emissions of CO₂. To achieve this, the capital intends to transform the urban fabric by investing in the construction of mixed-use structures. It is within the framework of the development of this large-scale project that Soletanche Polska has just completed the complex work of one of the mixed-use structures: Norblin Factory.
The project is located on the site of the former Norblin metal plated goods plant at the junction of two streets Prosta and Żelazna in the city’s inner Wola district. Norblin Factory will comprise more than 66,000 sqm of usable space, out of which 40,000 sqm will be offices. The remaining 26,000 sqm will include several functions, including restaurants, entertainment, culture, services and shopping. The tenants will include a boutique cinema, a BioBazar food market with certified organic products, a food hall with over 20 restaurant concepts, the Piano Bar with live music, and a restaurant on the building’s highest floor with a view onto central Warsaw. A four-level underground parking with 720 car parking spaces and 200 dedicated places is also to be provided. The project has been BREEAM pre-certified with a ‘Very Good’ rating for the design phase. To document the history of the former metal-plating plant on Żelazna street, the investor will establish the Open Museum of the Former Norblin Factory.
Mix of technologies – jet grouting, micropiles and diaphragm walls
The project assumes that the historic facades of the former factory will be integrated into the fabric of the new facility. The task of Soletanche Polska was to secure the stability of the historic walls by building up their foundations. 1423 columns were executed in jet grouting technology (977 as foundation reinforcement and protection of excavations, and 446 as soil reinforcement). The length of the columns ranged from 2 to 17 meters, and they were made inside and outside the buildings. A big challenge here was the limited space/gauge as well as the tight gaps between the buildings, which meant that the construction of the columns required time and great precision.
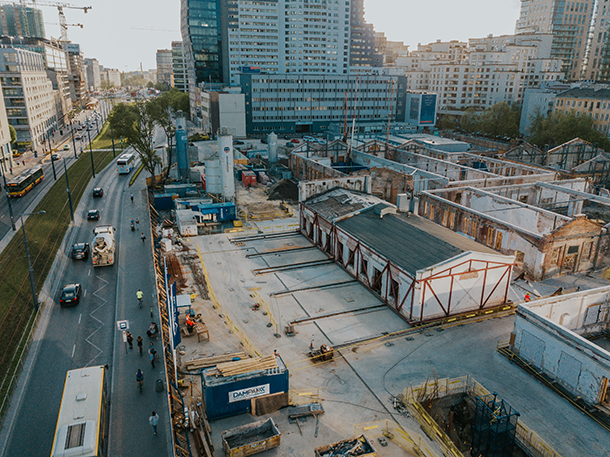
4-storey car park under historic buildings
Another big challenge was the implementation of foundation for the demanding above-ground structure and the construction of diaphragm walls, which have a triple function here: walls of a 4-story underground car park, retaining structure and a foundation supporting the above-ground structure. Soletanche made 18 672 m² of 80 cm thick diaphragm walls, which are the lining of the excavation and the walls of the underground car park. The deepest sections of diaphragm walls reach up to 48 m deep. Barettes – 197 units with a depth of 27 m – were executed using the same technology, which cooperate with the foundation slab. As part of the contract, Soletanche also made temporary pillars that support the ceilings of the parking lot’s floors during the excavation and reinforcement works.
The construction of diaphragm walls was one of the most difficult elements of the geotechnical puzzle. Not only due to the proximity of historic walls, but also due to the location of 3 buildings, which were to be laid on the foundation slab of the ceiling 0 and were located in the outline of the future underground parking lot. These circumstances made it necessary to use non-standard solutions, i.e. moving one of the buildings (building B-15 weighing 900 tons) and suspending two buildings (B-17 and B-18 with a total weight of 750 tons).
La construction des parois moulées a été l’une des principales difficultés de ce puzzle géotechnique. Non seulement les murs historiques étaient proches, mais trois bâtiments étaient situés au-dessus du futur parking et devaient être posé sur la dalle du rez-de-chaussée. Ce contexte exigeait des solutions exceptionnelles, c’est-à-dire déplacer l’un des bâtiments (B-15, pesant 900 tonnes) et suspendre les deux autres (B-17 et B-18, d’un poids total de 750 tonnes).
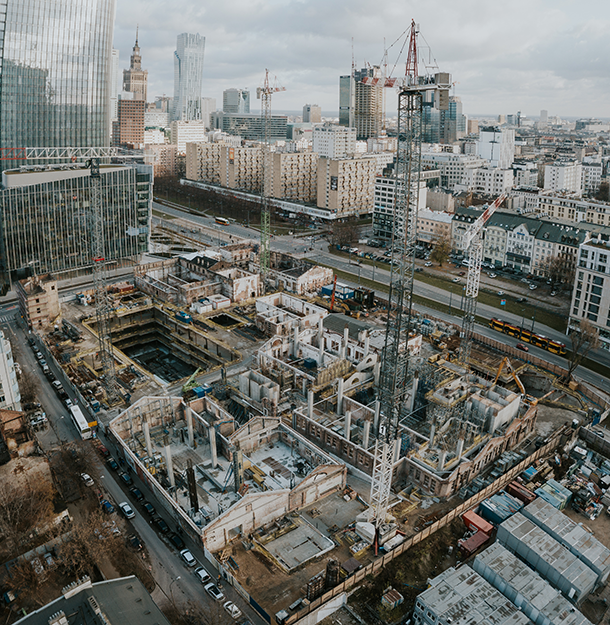
Levitating buildings
Two of these structures, building B-17 and B-18 had to be “suspended” so that the 0-floor slab could be constructed underneath them. 84 micropiles, reinforced by HEB profile, were used for this task. A steel cap was made on the micropiles, to hold the buildings and transfer the loads to the micropiles. Then, the building was excavated to the appropriate elevation and a reinforced foundation slab was made on which the building was ultimately laid as final
Why was the B-15 building moved?
As the works related to securing stability of historical building was following at the same time diaphragm walls were executed. At some point, the B-15 building “collided” with the construction of the diaphragm wall. The clearance between the buildings was too small for the crane to perform the last sections of the diaphragm walls that is why there was a need to move this building for the time of d-walls implementation.
The foundation works took 1.5 years. Safety and precision were throughout the entire project a high priority.