30/05/2023
Wellington Town Hall – Heritage meets Skill, Innovation and Challenge
The Wellington Town Hall is a Heritage listed orchestral hall located in New Zealand’s capital city, Wellington. It was constructed in 1904 to the standards of the day. The 2012 Christchurch earthquake and more recent seismic events, such as the 2017 Kaikoura earthquake, in the region has forced its closure since 2013. Extensive seismic strengthening has been commissioned as part of a wider redevelopment of the site to preserve this iconic building that forms a special part of New Zealand’s history.
March Construction was engaged by the main contractor Naylor Love to develop solutions to the subterranean aspects of the redevelopment. The project required the construction of a new underground corridor that would link into a future auditorium basement. Both inground structures had to be built in and around the existing building.
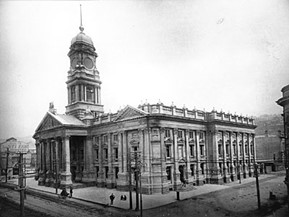
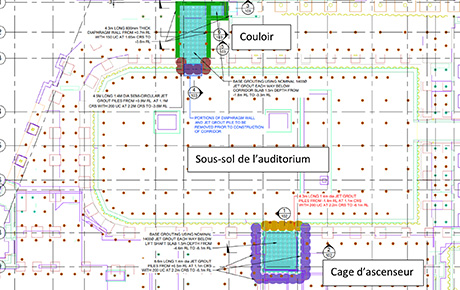
Stage 1 – Jet Grouting for the subterranean corridor and lift shaft
Due to sequence constraints, depth of excavation, and the limited working room available at the location of the corridor and shaft, a secant jetgrout column solution was developed. These columns were installed as part of the first stage at the end of 2021.
In addition to the challenges presented by the site, the team also had to contend with border restrictions due to COVID which severely limited our ability to utilize group technical input. Due to the close proximity to very sensitive heritage assets, the groups patented Jet+ single fluid system was implemented by March to install the 1200 and 1400mm diameter columns, as the single fluid system presented less risk of causing heave to the adjacent structures.
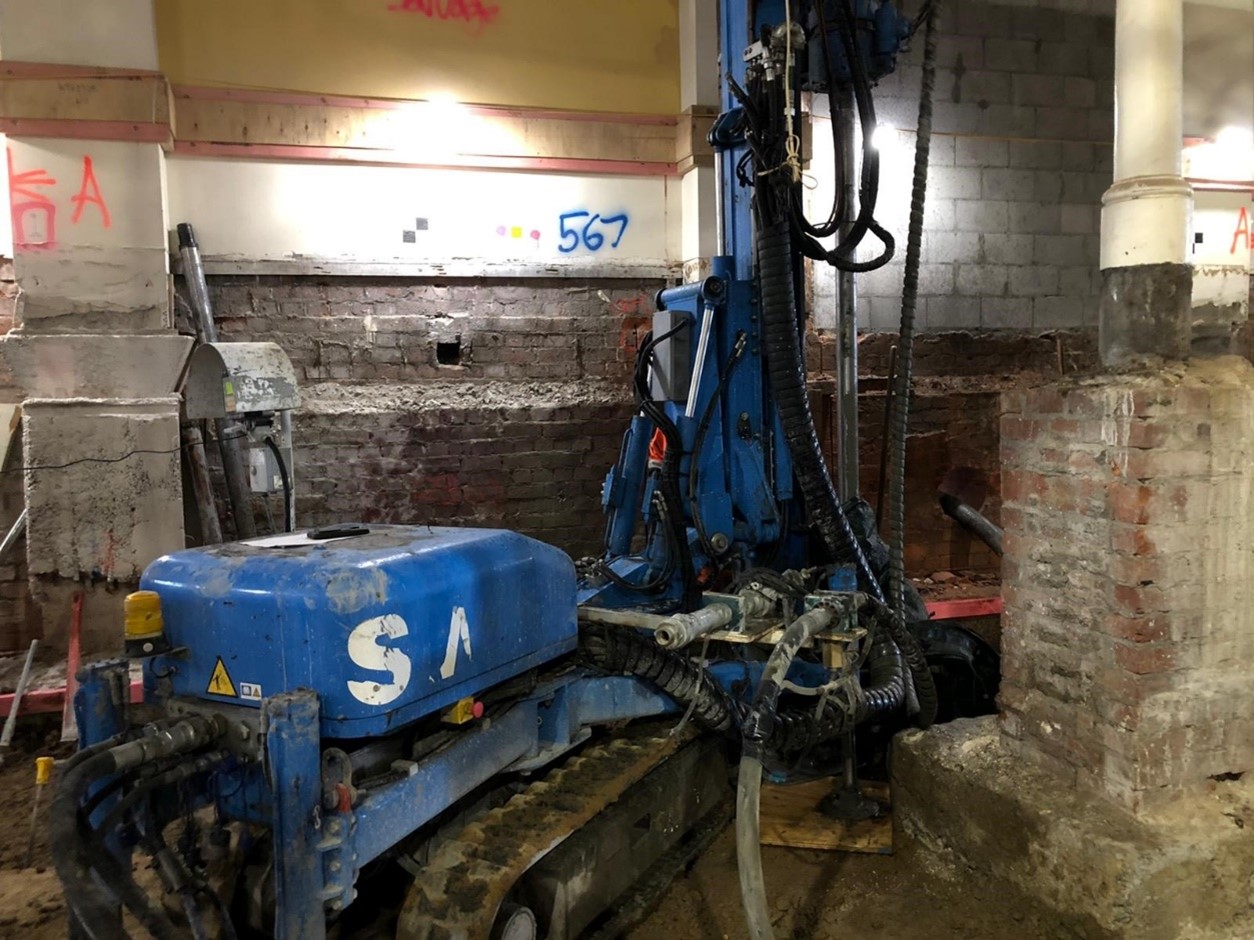
Stage 2 – Sheet piling and dewatering for the main auditorium basement
The client’s geotechnical designer had already progressed and consented a retention system for the auditorium basement utilizing sheet piles. As the main building would be relocated onto base isolated bearings at the time of installation, vibration from this activity was not considered likely to damage the structure, thus allowing this relatively cost effective method to be implemented.
The sheet piling phase of project was rather complex due to several factors, the most notable is the low headroom and protection of the existing structure (see photographs). The project required the installation of mostly 6 metre sheet piles and in some isolated areas 7 metres.
With the main challenge in the sheet pile install stage being the low headroom, the solution to overcome this was to cut all the sheets into 3m sections. The methodology was to then drive the 3m lead sheets and then structurally weld the additional 3m and repeat the driving process to meet the required design depth. The headroom that we were working in was approximately 5.8m.
With the restricted headroom that we were required to work in, an emphasis was put on the protection of the heritage components of the structure. March’s onsite team in conjunction with the Christchurch workshop looked at innovative ways we could do this. The preferred option was the placement of a sensor on the boom of the excavator, if this was to encounter the overhead structure an alarm would sound in the cab of the excavator.
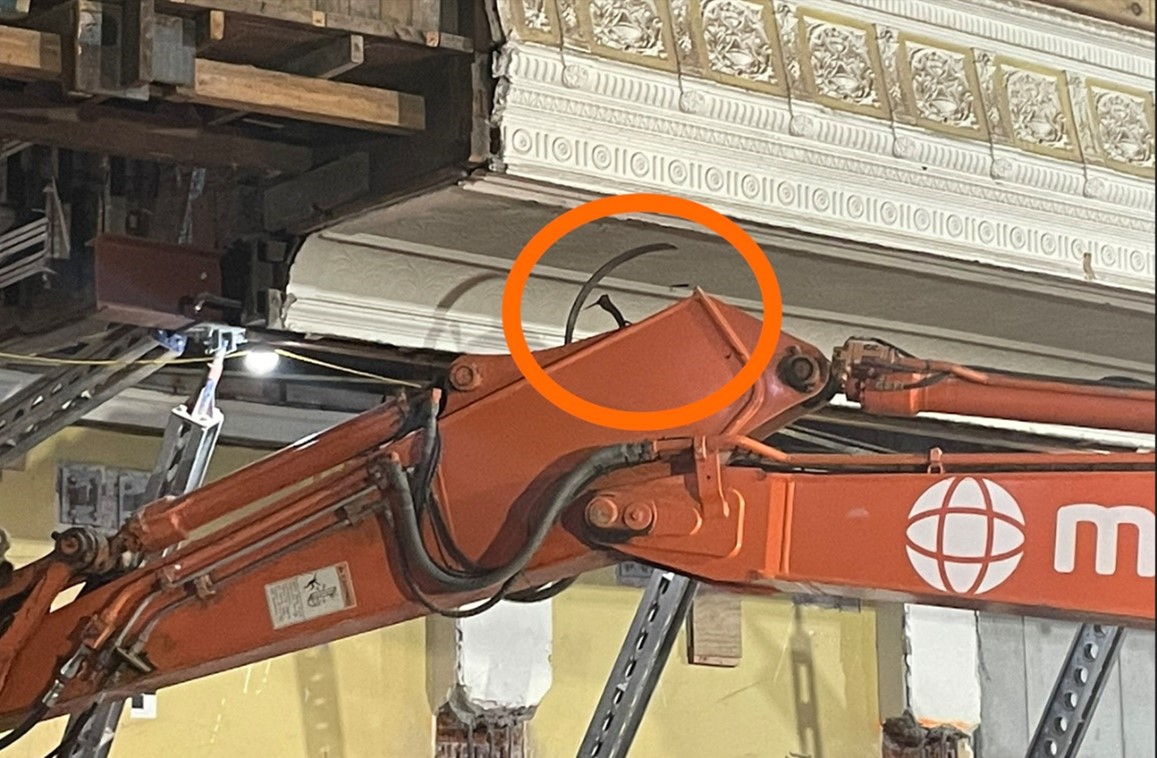
All sheets were installed with minimal difficulty, apart from some of the 7m sheets, however they were deemed adequate by the engineer. One of the clients major concerns and risks was in ground obstructions due to the age and lack of detail available around the original build some 100+ years ago. Luckily, only one obstruction was encountered and it was an old pile that we were able to remove.
The methodology of driving sheet piles may seem rather uncomplicated but this job was far from that and posed numerous challenges (see photographs) and required a skilled crew to complete this without incident.
To seal the sheet piles at the points where they interface with the existing structure, Tube a Manchette (TAM) grouting was opted for at these interfaces.
A 310UC97 whaler beam is required to be installed directly on top of the sheets and will carry all the swing tubes for the dewatering wells.
The dewatering system developed for this project consists of installing approximately 70 wellpoints at 1.8m centres around the site to draw the water down to a satisfactory level to allow for the 2.8-3.6m excavation from the top of sheets across the site.
To date, all the sheet piles have been completed and TAM grouting is ahead of schedule and are moving on to the wailer beam and dewatering portion of the works.