20/12/2019
Ejecución de 1000 columnas de Soil Mixing en la obra de la estación Pont de Sèvres, en el lote T3A del Grand Paris Express
Después de un verano marcado por un primer muro pantalla anclado por tirantes de fibra de vidrio y la instalación de muro berlinés, las obras especiales de la estación Pont de Sèvres, en el lote T3A del Grand Paris Express, adquieren una nueva dimensión. De hecho, en el inicio del otoño trae aparejado el comienzo de los trabajos de Soil Mixing para la estructura de la estación.
La operación consiste en un mejoramiento general de suelos dentro de la futura estación, para aumentar significativamente el número de puntales frente a los muros pantalla, durante la excavación. Efectivamente, el muro pantalla perimetral de la estación (con un espesor 1.5 m y una profundidad de 45 m) que está clavado en roca caliza no fisurada, se encuentra con un frente de roca caliza alterada de gran espesor, de 15 a 39 m de profundidad, y con pobres características geomecánicas.
Además, la fuerte presión de la tierra y el agua produjeron excesivas deformaciones en la pantalla durante las excavaciones.
Para garantizar el control de las deformaciones, el contratista principal había planeado 17 muros de contención en muros pantalla de 1.5 metros, que cubrieran el espesor de la roca caliza fisurada (frente a cada panel) y por los que debería pasar la tuneladora antes de iniciar la excavación de la estación.
El consorcio Horizon trabajó en conjunto con Soletanche Bachy Fondations Spéciales (SBFS) (subcontratista del consorcio) y la oficina de diseño y estudios de Eurofrance, para proponer una adaptación técnica que consiste en reemplazar estos muros de contención por un tratamiento general del suelo basado en Soil Mixing, que es más económico y reduce el riesgo de atascamiento para la tuneladora.
Para lograr la aprobación de esta solución, en marzo de 2019, se llevó a cabo una prueba en una parcela del sitio, en la que se instalaron 15 columnas de Soil Mixing y se realizó una prueba geotécnica a gran escala en elementos testigo tomados del núcleo del material tratado. La mezcla suelo / cemento de las muestras es similar a un concreto de suelo con resultados de resistencia a la compresión del orden de 3 a 6 MPa.
Como los resultados de las pruebas fueron concluyentes, la solución puede ahora implementarse a gran escala en todo el sitio de la obra.
Con este propósito, a fines de octubre, se instaló en un taller de Boulogne-Billancourt, a orillas de la Sena y frente a la isla Seguin, la perforadora SBFS Fundex F5000. La máquina está equipada con herramientas especialmente diseñadas y construidas para el proyecto entre los departamentos de materiales de Soletanche Bachy y del constructor IHC. Esta perforadora consta de una cabeza giratoria doble, que impulsa dos hileras de varillas equipadas con cuchillas de mezcla en su parte inferior (11 m de altura). Así, en cada pasada, la perforadora produce dos columnas de 1.5 m de diámetro, ligeramente intersectadas, y de 39 m de profundidad.
La inyección de lechada de bentonita / cemento se realiza en el descenso, a partir de los 15 m de profundidad (entrada en la piedra caliza), a través del núcleo hueco de las barras de perforación. La perforadora se alimenta durante toda la construcción de la columna mediante dos bombas de concreto, que se cargan en la planta de lechada. La planta se dimensionó para proporcionar un caudal de 80 m3 de lechada de cemento por hora, proporcionando una dosificación de 560 kg / m3 (C/E = 0.7). Para lograrlo, un digestor modular produce un lodo madre que se almacena en una alberca y que dos bombas Moritz 3000 dosifican según sea necesario. Todo se alimenta de agua bombeada del río Sena.
La perforación se realiza agregando aire comprimido a la línea de herramientas y se monitorea por medio de un sensor de deflexión que se encuentra a pie del barreno. La computadora incorporada en la máquina también permite controlar la mezcla correcta de suelos y verificar la penetración en vivo en la roca caliza no fisurada según los criterios de anclaje. Así, la profundidad de tratamiento del suelo puede optimizarse al producir cada par de columnas.
Los datos de la computadora se descargan en la nueva aplicación en línea de Zetta-Lyze para que el equipo del sitio los procese de manera continua. Las diagrafías de perforación y el modelado 3D de las desviaciones de las columnas pueden generarse casi en tiempo real.
Después de un período de ajuste y entrada en ritmo, el equipo organizado en dos puestos encontró su velocidad de crucero, produciendo de 8 a 14 “dobletes” (28 columnas) por día. Estos buenos resultados recompensan el meticuloso trabajo de preparación en el que han participado muchas áreas de la empresa (SBFS, por supuesto, pero también la oficina de diseño de materiales, el laboratorio de materiales, la dirección técnica del Grupo, los expertos, la oficina de diseño y estudios de Eurofrance y el equipo del sitio T3A).
Para febrero de 2020, se habrá producido un total de 504 dobletes ligeramente intersectados (unas 1008 columnas).
Inmediatamente después del Soil Mixing, los equipos de muros pantalla que trabajan actualmente en el corredor de conexión de la estación, ubicado a un lado, se ocuparán de instalar los muros pantalla de la estación. Según los planes, tres cucharas KS, organizadas en tres puestos, estarán a cargo de esta tarea durante la primavera de 2020. Finalmente, el muro pantalla del recinto y el tratamiento de Soil Mixing quedarán unidos por medio de una junta de jet grouting.
A partir de ese momento, la estación estará lista para permitir el paso de la tuneladora, que deberá comenzar su recorrido desde el pozo de lanzamiento en enero de 2020.
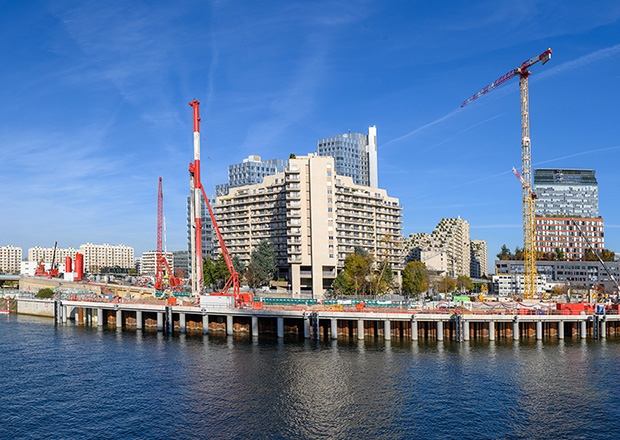